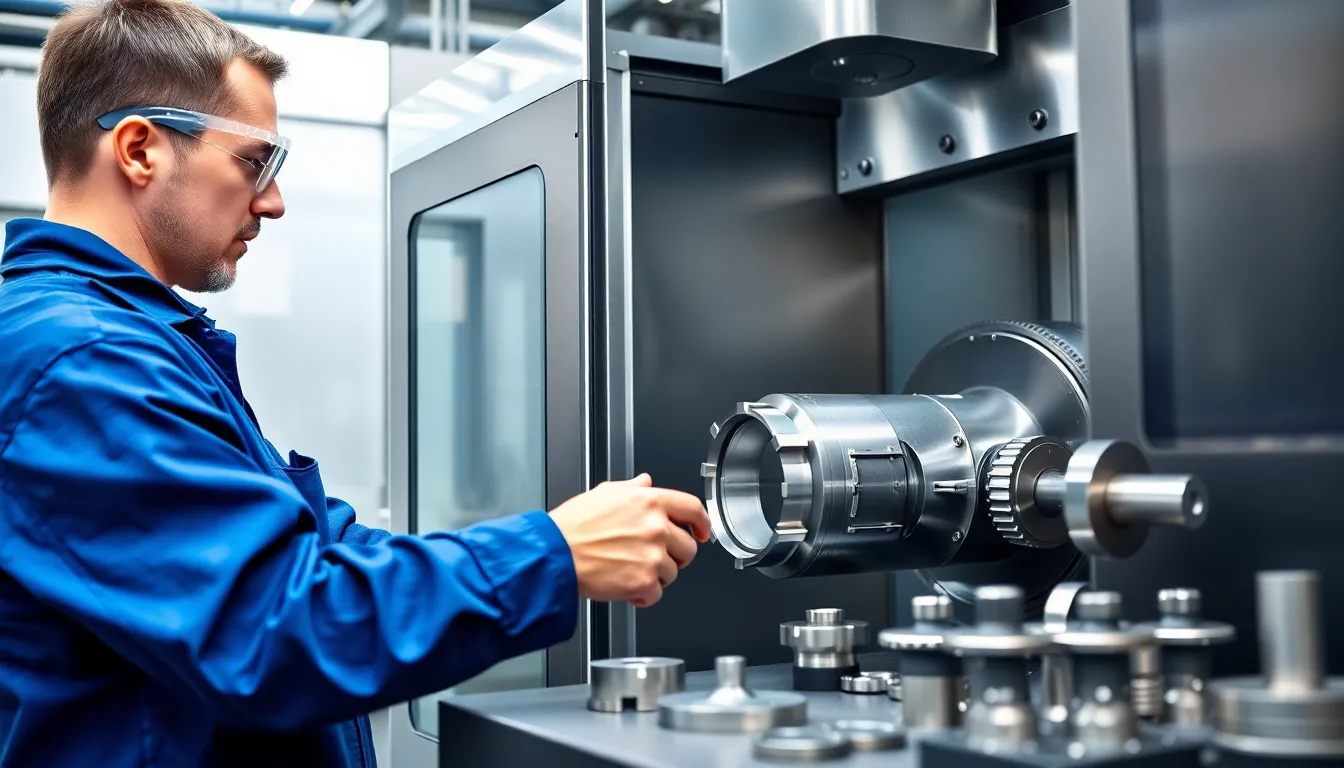
Key Takeaways
- CNC machining is essential in aerospace for producing highly precise, complex components from advanced materials like titanium, aluminum, and Inconel.
- The technology ensures tight tolerances, repeatable quality, and compliance with industry standards such as AS9100, which are vital for flight safety and performance.
- Aerospace CNC machining leverages multi-axis systems, real-time monitoring, and integration with digital CAD/CAM tools to handle intricate geometries and rapid prototyping.
- Key materials used include aluminum alloys, titanium, stainless steel, and magnesium, each chosen for their strength-to-weight ratios and resilience under extreme conditions.
- Manufacturers face challenges with material machinability and strict tolerance requirements, using advanced methods like adaptive machining and automated inspection to maintain precision.
- Ongoing innovations—such as 5-axis machining, AI-driven automation, and connected workflows—further enhance efficiency, accuracy, and traceability in aerospace parts production.
CNC machining aerospace parts ensures precision manufacturing of critical components from advanced materials like titanium, aluminium, and Inconel alloys. These computer-controlled processes achieve extremely tight tolerances of ±0.001 inch, essential for flight safety and performance standards. Multi-axis systems enable complex geometries whilst automated quality monitoring maintains consistency. Leading manufacturers such as Yijin Hardware specialise in producing high-precision aerospace components that meet stringent industry requirements for commercial and military applications.
Understanding CNC Machining in Aerospace
CNC machining in aerospace manufacturing applies computer-controlled equipment to produce high-precision parts from robust materials like titanium, aluminum, and Inconel. Manufacturers select CNC processes in aerospace to shape and drill components such as engine housings, landing gear elements, and complex brackets with tolerances as tight as ±0.001 inches. Multiple-axis CNC machines (usually 3-axis to 5-axis) support the intricate geometries and surface finishes that aerospace industry standards require.
Aerospace quality management relies on established standards like AS9100, which guide CNC machining operations to meet reliability and traceability benchmarks. Companies use real-time monitoring and digital controls to confirm every aerospace part meets dimensional accuracy and material integrity specified by industry regulators and aircraft manufacturers. For example, turbine disks, compressor rings, and airframe connectors produced via CNC sustain demanding load, temperature, and fatigue cycles during flight.
CNC machining in this sector increases production efficiency by enabling repeatable manufacturing and rapid prototyping of parts for both commercial and military aircraft programs. Manufacturers located in aerospace hubs, including specialists such as Yijin Hardware in Homestead, FL, deploy automated CNC processes to deliver precision aerospace components that support structural, propulsion, and avionics subsystems.
Key Materials Used in CNC Machining Aerospace Parts
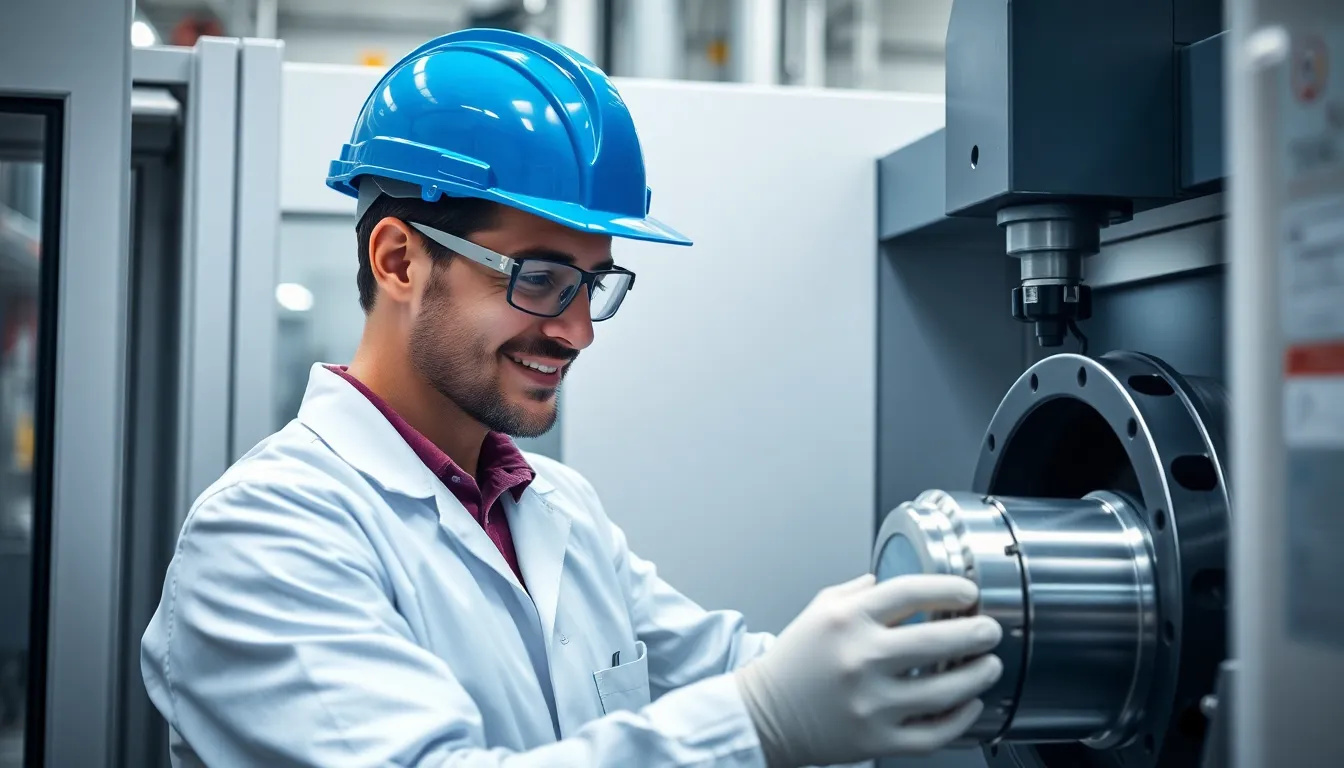
Aluminum and aluminum alloys supply high tensile strength, low density, and corrosion resistance essential for aerospace structures. CNC machining processes work well with alloys like 7075 (for wings, fuselage, and supports), 6061, 4047 (for cladding), and 6951. These materials appear in structural frames and load-bearing components, offering superior machinability and light weight required for flight.
Titanium and its alloys offer an exceptional strength-to-weight ratio, withstand extreme temperatures, and demonstrate notable corrosion resistance. CNC machining creates jet engine parts, airframes, and high-stress elements from titanium alloys, with examples including critical components for the Airbus A380, Boeing B787, F-22, and military helicopters. Machining titanium involves precise control of speed and heat to preserve tool life and achieve surface quality.
Stainless steel alloys such as grades 304 and 316 support parts where high strength, heat resistance, and corrosion resistance remain crucial. Engine components, landing gear, and actuation systems in aerospace applications rely on these alloys. Stainless steel withstands mechanical and thermal stresses, making it reliable for critical assemblies.
Magnesium’s status as the lightest structural metal enables its use in weight-sensitive applications like seat frames and luggage compartments. CNC machining produces magnesium parts for non-load-bearing features, maximizing efficiency and reducing overall aircraft weight. The excellent machinability of magnesium speeds up part production for such uses.
Material selection in CNC machining reflects each part’s function, operational stress, and exposure conditions. Aerospace manufacturers, including Yijin Hardware in Homestead, FL, use these advanced metals to achieve precise tolerances, preserve part integrity, and meet the reliability needed for commercial and military aircraft.
Advantages of CNC Machining for Aerospace Applications
CNC machining strengthens aerospace part production through unmatched precision, fast turnaround, and advanced customization features. Aerospace manufacturers like Yijin Hardware in Homestead, FL rely on CNC processes to deliver reliable, high-performance solutions for flight-critical components.
Precision and Accuracy
CNC machining achieves tolerances as tight as ±0.001 inch, crucial for aerospace components like engine casings and turbine blades operating in demanding conditions. Multi-axis control enables the production of complex geometries required for optimized aerodynamics and weight reduction. Yijin Hardware maintains AS9100-compliant quality standards, ensuring traceability and part consistency for every project. Real-time monitoring of production supports high dimensional accuracy and material integrity in each part.
Speed and Efficiency
Automation with CNC machining increases throughput, reduces lead times, and minimizes material waste—essential when using high-value materials such as titanium and aerospace-grade aluminum. Continuous operation limits human error and enhances repeatability for both prototyping and full-scale runs. Yijin Hardware’s automated systems handle mid to high-volume aerospace orders, reducing setup time by eliminating the need for unique tooling per part.
Customization Capabilities
Integration of CAD software with CNC equipment supports rapid design changes, frequent prototyping, and tailored parts for evolving aerospace needs. CNC machining at Yijin Hardware enables the fabrication of intricate parts needed for next-generation propulsion and structural systems. Each part matches customer specifications while meeting strict industry standards for consistency, quality, and performance. Engineers quickly adapt and optimize designs throughout the part lifecycle using digital manufacturing techniques.
Challenges in Manufacturing Aerospace Parts with CNC Machining
CNC machining aerospace parts brings unique difficulties due to strict quality and engineering standards. Key challenges relate to material properties, geometric complexity, and inspection precision.
Material Constraints
Machining aerospace parts involves processing advanced materials such as titanium alloys, Inconel, and carbon fiber composites. These materials, selected for high strength and temperature resistance, are difficult to cut due to factors like brittleness and work hardening. Tool wear escalates when machining titanium or Inconel, for example, leading to higher production costs. Specialized processes—waterjet cutting, laser-assisted machining, and cryogenic machining—combat heat damage and delamination. Manufacturers like Yijin Hardware apply these methods to maintain part integrity and production efficiency, ensuring that even complex structures withstand the operational stresses of flight. According to industry sources, tool life drops by up to 70% for some superalloys compared to standard steels.
Tolerance and Quality Control
Meeting tolerance requirements underpins all CNC machining for aerospace. Many parts, including turbine blades and brackets, require tolerances tighter than ±0.001 inch. Achieving these demands multi-axis machines, advanced CAD programming, and strict control of every process step. Quality assurance extends beyond measurement to certified standards like AS9100. Inspection equipment such as coordinate measuring machines (CMMs) and laser scanners confirms dimensional accuracy immediately after production. Yijin Hardware integrates real-time monitoring and non-destructive testing to provide consistent, traceable quality for aerospace clients. Any deviation outside established limits risks functional failure, making repeatability and inspection accuracy central concerns on every order.
Latest Technologies Enhancing CNC Machining Aerospace Parts
CNC machining for aerospace parts relies on advancing technologies to deliver complex shape accuracy and meet rising industry standards. Enhanced automation, digital integration, and smarter software drive new production capabilities.
Advanced Tooling and Automation
Multi-axis machining, including 5-axis and higher, enables precise, intricate part production for aerospace applications such as turbine discs and compressor blisks. Adaptive machining dynamically adjusts operations based on real-time sensor feedback, reducing tolerance drift and scrap. Robotics and automation, powered by AI and machine learning, handle repetitive tasks, drive predictive maintenance, and monitor production through sensor networks. Connected manufacturing systems link CNC machines to production planning and quality control with real-time digital communication. Companies like Yijin Hardware in Homestead, FL use these technologies for efficient, data-driven workflows, faster part turnaround, and quality assurance.
Integration of CAD/CAM Software
Modern CAD/CAM platforms directly automate CNC toolpath creation from detailed 3D engineering models. Machine learning algorithms within these systems analyze design data, optimize tool movement, and adjust machining parameters to minimize waste and improve surface finish. AI-enabled CAD/CAM reduces manual programming errors and accelerates design-to-production cycles. Integrated software environments allow seamless data exchange between engineers and machinists. At Yijin Hardware, advanced CAD/CAM integration supports rapid prototyping and precise machining of aerospace-grade alloys, achieving tight tolerances consistently for aerospace components. This digital workflow results in faster delivery, fewer rejects, and greater traceability across the production cycle.
Case Studies: Successful CNC Machined Aerospace Components
Case studies highlight successful CNC machined aerospace components which rely on advanced equipment to meet exacting requirements.
- Large Engine Impeller by WayKen
Engineers produced a forged aluminum alloy (AL 6061 ASTM B247) impeller with a nearly 500mm diameter and 300mm blade height. Tolerances included a surface roughness of Ra 3.2μm and 0.02mm concentricity on the central shaft hole. Machining utilized 5-axis CNC turning and milling, as well as Electrical Discharge Machining (EDM). Production delivered 9 pieces in 18 business days. Results achieved extreme precision for a high-stress aerospace engine application.
- TurboTech Multi-Axis CNC
Technicians operated 5-axis CNC machines to manufacture complex engine and structural parts in aviation. Parts met tight tolerance requirements with improved throughput and manufacturing efficiency, showing the role of multi-axis technology in meeting modern industry demands.
- Yijin Hardware Aerospace Applications
Yijin Hardware in Homestead, FL, manufactures high-precision aerospace brackets and turbine blades using multi-axis CNC machining and automated quality monitoring. Production consistently achieves tolerances to ±0.001 inch on aerospace-grade metals like titanium and aluminum alloys. Each batch is validated using digital measurement equipment for traceability and dimensional accuracy.
Component | Material | Key Specs | Machining Processes | Company | Lead Time |
---|---|---|---|---|---|
Large Engine Impeller | AL 6061 ASTM B247 | 500mm Ø, Ra 3.2μm, 0.02mm concentricity | 5-axis CNC, EDM | WayKen | 18 days |
Turbine Blades, Structural Brackets | Titanium, Aluminum | ±0.001 inch tolerance | Multi-axis CNC, Automated Monitoring | Yijin Hardware | Project-specific |
Complex Engine/Structural Parts | Aerospace-grade metals | Tight tolerances, complex shapes | 5-axis CNC | TurboTech | Not stated |
About Yijin Hardware
Yijin Hardware, located in Homestead, FL, is a leading provider of precision manufacturing services, specialising in CNC machining, sheet metal fabrication, and custom fasteners.
Under the leadership of CEO Gavin Yi, Yijin Hardware also offers additional solutions such as die casting, injection molding, and 3D printing to support various industries, including automotive, aerospace, medical, and energy. With a commitment to high-quality manufacturing and precision engineering, Yijin Hardware delivers tailored solutions to meet the unique needs of its clients.
Contact:
Gavin Yi, CEO
Phone: +1 626 263 5841
Email: [email protected]
Website: www.yijinsolution.com
Follow us:
Location:
760 NW 10th Ave, Homestead, FL 33030
Frequently Asked Questions
What is CNC machining, and why is it important in aerospace engineering?
CNC (Computer Numerical Control) machining is a manufacturing process that uses computer-controlled equipment to create precise parts. In aerospace engineering, it’s essential because it allows for the creation of complex components from high-strength materials, meeting strict industry standards for safety, performance, and reliability.
Which materials are commonly used in aerospace CNC machining?
Common materials include aluminum and its alloys (for their strength and corrosion resistance), titanium alloys (for critical parts that require strength and low weight), stainless steel (for heat-resistant components), and magnesium (for lightweight, non-load-bearing parts).
How precise is CNC machining for aerospace parts?
Aerospace CNC machining can achieve extremely tight tolerances, often as close as ±0.001 inch. This level of precision is crucial for safety-critical components that must perform reliably under demanding conditions.
What are some examples of aerospace components made with CNC machining?
Typical aerospace components made with CNC machining include turbine blades, structural brackets, engine impellers, airframe parts, and landing gear components—each requiring high precision and durability.
How does CNC machining ensure quality and consistency in aerospace manufacturing?
CNC machining uses advanced machinery, real-time monitoring, and strict quality management standards like AS9100. Inspection equipment such as coordinate measuring machines (CMMs) confirms dimensional accuracy and material integrity for every part produced.
What are the main benefits of CNC machining in the aerospace industry?
CNC machining offers unmatched precision, fast turnaround, advanced customization, increased production efficiency, and minimized material waste. Automation and CAD/CAM integration further streamline workflows and enable rapid prototyping for evolving aerospace needs.
What challenges are faced in CNC machining for aerospace applications?
Challenges include working with difficult-to-machine materials like titanium and Inconel, meeting tight tolerances, adhering to strict industry regulations, and maintaining consistent part quality. Advanced processes and rigorous quality control are essential to overcoming these hurdles.
How are advanced technologies improving CNC machining for aerospace?
Technologies like multi-axis machines, robotics, AI-driven automation, and modern CAD/CAM software enhance precision, throughput, and quality. Connected manufacturing systems ensure real-time communication for better traceability and quality control.
How does CNC machining impact production efficiency for aerospace companies?
CNC machining reduces lead times by automating processes, allowing for reliable repeatability, and enabling rapid prototyping. This streamlines production for both commercial and military aerospace projects while maintaining strict quality standards.
Can you provide examples of successful aerospace CNC machining projects?
Yes. Case studies highlight projects like WayKen’s engine impeller using 5-axis CNC, TurboTech’s efficient multi-axis CNC manufacturing, and Yijin Hardware’s high-precision brackets and turbine blades—all demonstrating tight tolerances and consistent quality.